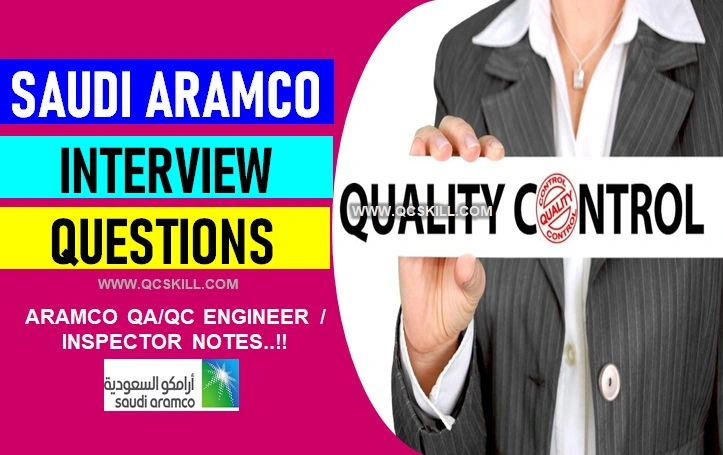
QC Notes Level-26
Quality Systems interview Questions
- Describe the difference between QA & QC?
- Answer: Quality Control is the operational techniques (Inspection, Examination & Testing) that are used to fulfill requirements for quality. Quality Assurance is the system of action and planning needed to provide confidence that a Product or Service will satisfy quality requirements
- What do quality system audits evaluate?
- Answer: The degree of quality system conformance to established requirements.
- Saudi Aramco has adopted the basic framework and definitions of the International Quality System Standards ISO-9000 Series. This has been done to provide universal understanding and improve communication between the COMPANY and prospective CONTRACTORS whose Quality System is congruent with the ISO-9000 Series. Describe the basic elements of an ISO 9000 Series Quality Program?
- Answer:
- Quality Management & Quality Assurance Standards per ISO-9000
- Quality Systems per ISO-9001, 9002, 9003
- Quality Plan Guidelines per ISO 10005
- What is an essential variable as related to a Welding Procedure Specification (WPS)?
- Answer: A change in a welding condition that will affect the weld’s mechanical properties.
- What is the relationship between a Procedure Qualification Record (PQR) and a WPS?
- Answer: The PQR documents what occurred during the welding and testing of the test coupon.
- Heat input (SMAW per ASME IX) is a combination of what two electrical characteristics & travel speed?
- Answer: Voltage and Amperage
- Excessive heat input is mainly attributed to what poor welding techniques during SMAW process?
- Answer: Excessively wide weaving and slow travel speed.
- What are 3 potential sources of Hydrogen encountered during SMAW process?
- Answer: Moisture in the metal and electrode coating, oil, elemental Hydrogen in the base metal
- What are several likely causes of porosity in carbon steel welds using the SMAW process?
- Answer: Poor welding technique and equipment, excessive wind, moisture & weld contaminants.
- What dimension is measured to determine the size of a concave fillet weld?
- Answer: Throat
- If a product is to be stress relieved, why is it important to use exactly the same RT procedure before and after stress relieving?
- Answer: So that a baseline evaluation is performed to ensure that borderline indications are not misinterpreted after stress relief.
- What dimension is measured to determine the size of a convex fillet weld?
- Answer: Leg
- Where would cracking most likely occur from excessive current input in a single pass weld?
- Answer: Centerline of the weld
- Using GTAW process, describe what happens to a weld without proper purging/back gassing on SS material?
- Answer: Oxidation at the ID (Sugaring)
- Name 3 of the 5 mechanical tests in ASME IX employed for procedure & performance qualifications?
- Answer: Tension, Guided Bend, Fillet-weld, Notch-toughness & Stud-weld tests Mechanical/NDT (assume SMAW process used for all questions)
- How is Magnetic Particle inspection of a weld using the wet continuous test method performed?
- Answer: The particles (usually fluorescent) are sprayed, poured on or applied by immersion and the
magnetizing current is applied while the particles are still flowing.
- Indications with Liquid Penetrant Testing are easily seen if the surface has been prepared by grinding prior to testing? True/false? Why?
- Answer: False, because grinding can smear metal and mask/cover discontinuities.
- Name an NDT method and technique that employs a reflected sound beam that can be used for the volumetric examination of welds?
- Answer: Ultrasonic Testing using Shear Wave Technique provides good volumetric exam coverage.
- List 3 disadvantages of RT over other NDT Methods.
- Answer: Radiation Safety Precautions, Planar defects not readily detectable, Heavy
equipment
- If a product is to be stress relieved, why is it important to use exactly the same RT procedure before and after stress relieving?
- Answer: So that a baseline evaluation is performed to ensure that borderline indications are not misinterpreted after stress relief.
- A dark narrow area 2-3mm wide appears on a radiograph all along the edge of the area representing the weld. The joint has a 60* double-vee groove. What is the indication most likely to be?
- Answer: External Undercut
- A localized darker density Radiographic image with fuzzy edges in the center of the width of the weld image that may or may not be wider than the width of the root pass image is most likely what?
- Answer: Burn-through
- Name 5 common film artifacts that may be cause for rejection of Radiographic Film?
- Answer: Film Scratches, light leaks, chemical stains, fogged film, static marks, water marks, streaks, crimp marks, finger marks, lint, dirt
- When the radiation source is located inside piping with the film located outside, single-wall exposure and single-wall view, name this type of exposure?
- Answer: Panoramic
- How do gamma rays compare with X-rays when applied to RT of welds?
- Answer: Gamma rays have greater penetration ability, but give poorer contrast.
- Per ASME B31.3 (assume latest edition), name three of the four Categories of Fluid Service?
- Answer: Categories D, M, High Pressure & Normal
- Per ASME B31.3, who is responsible for classification of service to a given category?
- Answer: The Owner
- Per ASME B31.3 (assume latest edition), what are the RT requirements for Socket welds in severe cycle service?
- Answer: None
- Relating to the above question, Give good reasons why random RT of socket welds is recommended?
- Answer: Both gross welding defects & poor quality welders can be identified, with repairs and corrective action taken, & Gap can be verified.
- Briefly describe good QC practice relating to the installation & bolting of flanges?
- Answer: Verify Materials (type, size and rating) are acceptable, gasket verification & good bolting practices (torque value requirements met) in accordance with approved procedures.
- What is an often-overlooked Inspection/NDT requirement on the installation of an orifice flange?
- Answer: Visual weld inspection of the seal weld & NDT has been missed prior to bolting of flanges
- Per ASME Section VIII, Div. 1, can a nozzle to be attached to the exterior surface of a pressure vessel without any portion of the nozzle projecting into the shell?
- Answer: Yes, with many restrictions
- Explain the difference between a 2:1 Ellipsoidal head and a hemispherical head?
- Answer: A hemispherical head has no flange and knuckle region and holds greater volume.
- Which of the above two heads given equal thickness can withstand greater internal pressure?
- Answer: The 2:1 elliptical head can withstand much more internal pressure given equal thickness.
- In ASME Section VIII, Division 1, Parts UW and UCS cover what scope of work?
- Answer: UW designates requirements for pressure vessels and vessel parts fabricated by welding, and UCS designates requirements for pressure vessels and vessel parts constructed of carbon and low alloy steels.
- Name several Inspection items on internal component/tray installation for new columns?
- Answer:
- Drawings, Calcs & Data reviewVerification of Material Construction of Internal components (tray assemblies & systems, hardware, packing medium) Location, levelness and orientation of internal components per Mfg. Drawings/tolerances.
- Seams, holes, gaps, missing items, looseness of hardware in trays Leakage Tests as needed for trays, troughs, weirs, etc.
- Final Cleanliness of Tray Assemblies
- What API documents apply to the replacement of an existing floor for an Aboveground Oil Storage tank?
- Answer: API 653 & API 650
- What are two key items to be resolved prior to addition of new nozzles to older tanks per API 653?
- Answer: Tank Material identification, Material Design Considerations & selection (need for shell insert).
- Briefly describe an area impressed Cathodic Protection System?
- Answer: Electrical current & use of selectively placed sacrificial anodes is employed to stop/slow the electrochemical reaction that occurs during the corrosion process.
- Relating to Contractor Weld Shop evaluation prior to the beginning of pipe welding for a major project, what are several key items you would look for as the Inspector assigned to approve the shop for Company?
- Answer:
- 1. Manpower = Ensure adequate Personnel that are trained, qualified, certified & approved
- 2. Methods = Ensure that standards are followed and that welding procedures, special processes (PMI, PWHT, etc) are acceptable and that there is a good quality system (paper trail) in place.
- 3. Materials = Ensure Materials are approved, certified, documented (traceable), stored correctly with area for deficient items (quarantined), and segregation of dissimilar metals.
- 4. Machines = Ensure Equipment is adequate for the intended work and in good working condition.
- 5. Measurement = Ensure Contractor QC Program & testing/calibration program is in place for equipment and work.
- 6. Environment = Ensure that the working environment (building) is safe, sheltered from the elements and adequate to ensure quality work.
- Briefly describe good QC practice relating to the installation & bolting of flanges?
- Answer: Verify Materials (type, size and rating) are acceptable, gasket verification & good bolting practices (torque value requirements met) in accordance with approved procedures.
- Name several Inspection items on internal component/tray installation for new columns?
- Answer:
- Drawings, Calcs & Data review Verification of Material Construction of Internal components (tray assemblies & systems, hardware, packing medium)
- Location, levelness and orientation of internal components per Mfg. Drawings/tolerances.
- Seams, holes, gaps, missing items, looseness of hardware in trays Leakage Tests as needed for trays, troughs, weirs, etc.
- Final Cleanliness of Tray Assemblies
Continue QC Notes Level-27 ⭕ API 650 and 32-SAMSS-005 – Atmospheric Tanks
See More: Aramco Quality Standard
What is Aramco – Our Code of Business Conduct.PDF download
- Saudi Aramco Definition of Terms | Code
- eBook Welding QC Inspector Interview Questions & Answers Vol-1
- SAMSS Index Download Excel File Free
- Index SAES | Excel | Saudi Aramco Engineering Standards
- Aramco :: Pressure Vessel Reference, Installation Standards
- ARAMCO :: COMPUTER BASED TESTING (CBT)
- PUMP SKID DESIGN
- pump sizing calculator excel
- Centrifugal Pumps and Compressors Installation Standards
- Saudi Aramco form 175 inspection & testing requirement
- HAZOP Vs HAZID in the Oil & Gas Industry
- OIL & GAS PROJECTS CODES & STANDARDS
- Saudi Aramco form 175 inspection & testing requirement
- Saudi aramco form 175 download
FAQ:
How to prepare for a Saudi Aramco interview?
Your Saudi Aramco interview or interviews are likely to include many behavioural and technical questions, as well as those concerning your previous experience. We highly recommend using the STAR method to ensure that your responses are organised and thorough.
How do you answer the interview question about quality?
Explain how quality relates to the position you’re seeking
After you describe quality, explain how it relates to the position for which you’re interviewing. The answer might vary depending on the industry. Explain why it’s important and describe quality with industry examples.
What is the minimum salary in Aramco?
Minimum salary at Saudi Aramco depends on the role you are applying for. For Mechanical Technician the minimum salary is ₹1.6 Lakh to ₹8 Lakhs per year, and for Hvac Technician the minimum salary is ₹6 Lakhs to ₹7.5 Lakhs per year and so on.
Saudi ARAMCO a good employer?
Saudi Aramco has an overall rating of 4.3 out of 5, based on over 2,320 reviews left anonymously by employees. 85% of employees would recommend working at Saudi Aramco to a friend and 78% have a positive outlook for the business. This rating has been stable over the past 12 months.