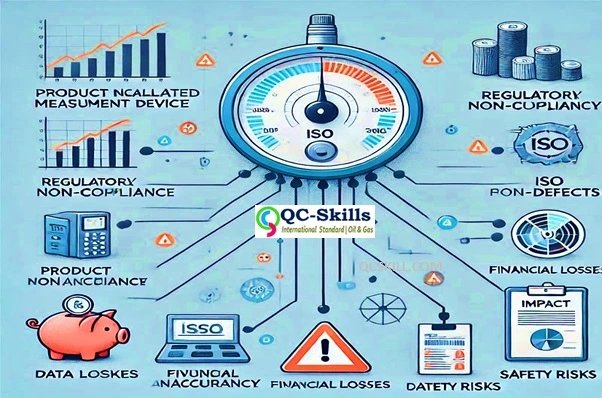
Calibration is often given high priority within organizations, especially where accurate measurement tools are essential for maintaining product quality, safety, and regulatory compliance. However, if calibration of instruments is neglected or given insufficient priority, the consequences can be substantial, particularly in a modern quality landscape where precision and consistency are critical.
Here are some of the ways insufficient calibration affects modern quality management:
1. Increased Risk of Product Defects
Instruments that are not calibrated correctly can lead to inaccurate measurements, causing defects that may go undetected during production.
Defective products can result in recalls, customer dissatisfaction, and potential legal issues, affecting both brand reputation and revenue.
2. Non-Compliance with Standards
Industry standards like ISO 9001 and ISO 17025 require regular calibration of instruments. Non-compliance can lead to failing audits, certification loss, and regulatory penalties.
Lack of adherence to calibration standards impacts the organization’s credibility and can even lead to contract terminations with clients who demand strict compliance.
3. Financial Loss from Process Inefficiencies
Uncalibrated equipment can lead to inefficient processes, causing higher rates of waste and rework due to inaccurate measurements.
In the long term, this increases production costs and reduces profitability, which may also impact the organization’s ability to invest in improvements.
4. Inability to Support Data-Driven Decision Making
Accurate measurement data is the foundation of quality control, process improvement, and decision-making. Without reliable data, analysis becomes flawed, leading to poor strategic decisions.
In quality improvement methodologies, such as Six Sigma and Lean, uncalibrated instruments make it impossible to trust data, leading to inaccurate conclusions and ineffective changes.
5. Impacts on Safety and Compliance in High-Risk Industries
For industries like aerospace, pharmaceuticals, and healthcare, uncalibrated instruments can pose direct safety risks. Inaccurate measurements in these fields can lead to critical failures, risking lives and significant legal liabilities.
Regulatory authorities impose strict penalties on safety violations, which can include facility shutdowns, product bans, and loss of operational licenses.
6. Challenges in Implementing Digital Quality and Quality 4.0
Modern quality relies on data analytics, automation, and real-time monitoring. Uncalibrated instruments compromise the accuracy of this data, creating barriers to implementing Quality 4.0 initiatives.
With inaccurate inputs, predictive maintenance and AI-based quality controls cannot function effectively, leading to a breakdown in digital quality initiatives.
In Summary:
Inadequate focus on calibration undermines the integrity of a QMS and limits an organization’s ability to meet modern quality demands.