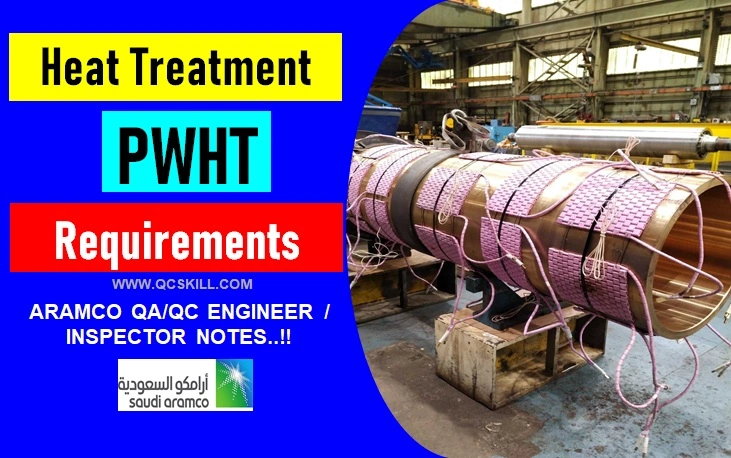
QC Notes Level-22
Heat Treatment & PWHT Requirements
✅ Introduction
- PWHT is required where there is a risk of environmentally-assisted cracking. PWHT of C-Mn steels is typically carried out at approximately 600°C, for one hour per 25mm of thickness.
- Equipment used for the PWHT should be suitable according to ISO 17663.
- The ASME B31. 3 code provides guidelines for piping fabrication in the process industry, including post-weld heat treatment (PWHT) requirements. Section 331.1. 1 outlines PWHT temperatures for various P-Number and group numbers, exemptions, and altered holding times.
- The post weld heat treatment is often usually after the union by welding of two material base such us carbon steels or alloy steels. Post weld heat treatment (PWHT) can be apply to one complete piece or locally, by applying only the heat treatment to the welded joint area.
- The need of PWHT is mostly due to residual stresses and microstructural changes that occur after welding. During the welding process, a high-temperature gradient is experienced between the weld metal and parent metal. Codes like ASME specify the specific requirements for PWHT of materials.
✅ PWHT (POST WELD HEAT TREATMENT)
Applied to some welded steels in order toensure that the properties of weldment will be suitable for intended applications often called Stress Relief:
- Intermediate Stress Relief = 600*C for 1 hour
- Dehydrogenation Heat Treatment = 350*C for 4 hours
- Specified PWHT area extending at least 6 times the thickness of the material
being welded but not less than 25mm from the edge of the weld, which is greater - If PWHT not perform in Furnace, insulation shall be applied 300mm on either side of the weld, insulation shall be remove before the temperature has cooled to 150*C
- Minimum soaking time shall be 1 hour per 25mm of thickness
✅ PWHT BENEFITS
- To improve the resistance of the joint to brittle fracture
- To improve the resistance of the joint to stress corrosion cracking
- To enable welded joints to be machined to accurate dimensional tolerance
✅ PWHT HEAT SOURCES
- Permanent or Semi-permanent furnace using gas or oil or electric heater
- Electrical Resistance Heater
- Induction Heater
✅ THERMOCOUPLE LOCATION IN FURNACE
- Thinnest major component
- Thickest member
- Top of the vessel
- Bottom of the vessel
- Temperature recorder shall be calibrated every 3 months or can be extended to 12 months with aramco approval
- Machine surfaces, flange faces, threaded bolt holes, threads, etc. shall be protected from oxidation it shall be coated with deoxiluminite or other suitable materials
- After completion of PWHT attachment areas shall be ground smooth, if specified by inspector areas shall be examined by MT or PT after grinding
12- SAMSS-008 – Enlargement of bolt holes shall be done by reaming or drilling only. Flame cutting or burning are not allowed (PIP STS05130, para. 6.7.3)
SAIC-W-2068 Welding Inspection on Vessel Fabrication
✅ Document required at welding station:
- All weld joint shall be marked for identification by a weld number & welder symbol and made with suitable weather proof marking material.
- The markings shall be placed in location such that they will be easily observed and remain visible for a time suitable for SAPID.
WELDING – ASME SEC.IX
- A weld – is a union of materials produced by heat and or pressure
- A joint – is a configuration of members
Types of Common Welds
- Butt weld
- Fillet weld
- Spot weld
- Seam weld
- Edge weld
Types of Common Joints
- Butt joints
- Tee joints
- Lap joints
- Open corner joints
- Close corner joints
Weld Preparation
- Single bevel butt weld
- Single vee butt weld
- Single J butt weld
- Single U butt weld
- Double bevel butt weld
- Double vee butt weld
- Normally made on thinner materials when access from both sides are restricted
- Double J butt weld
- Double U butt weld
✅ 5 Acceptable Heat Treatment of Process Piping:
- Enclosed furnace
- Local flame heating
- Electric resistance
- Electric induction
- Exothermic chemical reaction
Continue QC Notes Level-23 ⭕ Aramco :: Welding Inspector Responsibilities
See More: Aramco Quality Standard
- SAMSS Index Download Excel File Free
- Index SAES | Excel | Saudi Aramco Engineering Standards
- Aramco :: Pressure Vessel Reference, Installation Standards
- ARAMCO :: COMPUTER BASED TESTING (CBT)
- PUMP SKID DESIGN
- pump sizing calculator excel
- Centrifugal Pumps and Compressors Installation Standards
- Saudi Aramco form 175 inspection & testing requirement
- HAZOP Vs HAZID in the Oil & Gas Industry
- OIL & GAS PROJECTS CODES & STANDARDS
- Saudi Aramco form 175 inspection & testing requirement
- Saudi aramco form 175 download