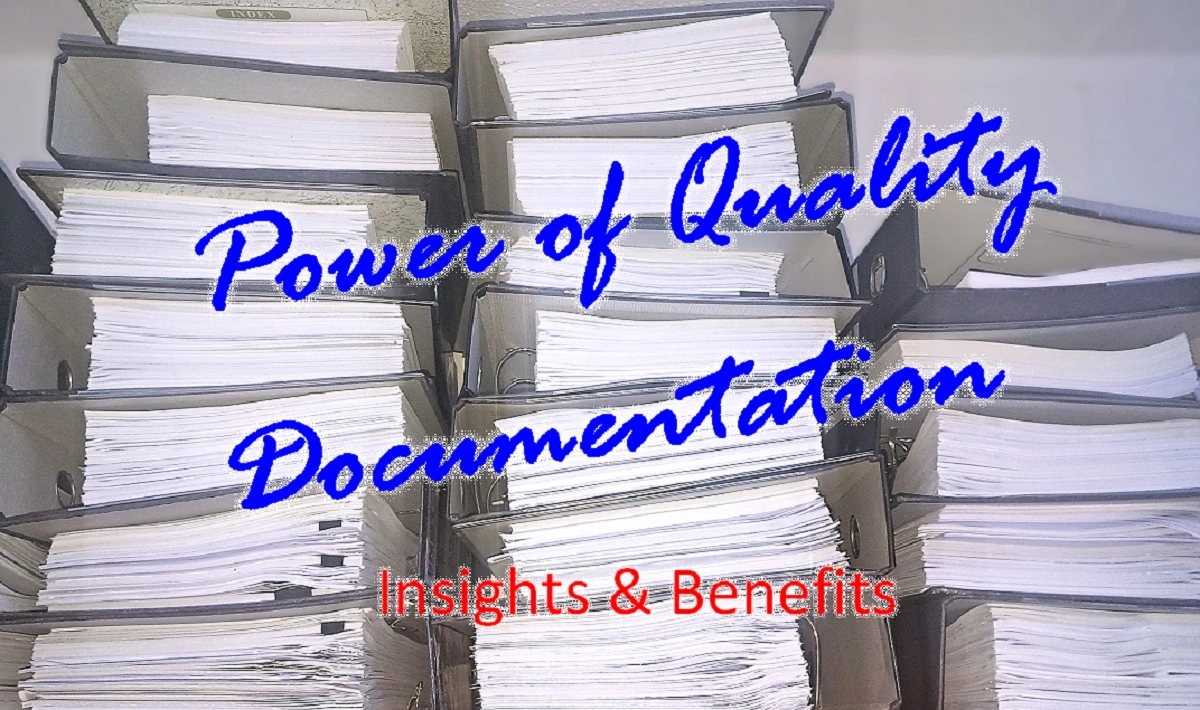
Why is Quality Documentation Essential?
In every industry, well-structured quality documentation is the key to standardization, compliance, efficiency, and continuous improvement. It provides clarity, minimizes errors, and ensures that processes run smoothly and consistently.
What Happens Without Proper Documentation?
- Process inconsistencies
- Compliance failures
- Increased risks & errors
- Inefficient operations
Key Benefits of Quality Documentation
- Ensures Standardization – Keeps operations consistent across teams.
- Regulatory Compliance – Meets ISO, GMP, FDA, HACCP, and other legal requirements.
- Enhances Training – Aids onboarding and skill development.
- Reduces Errors – Improves process reliability and safety.
- Drives Continuous Improvement – Enables audits, tracking, and optimization.
The Quality Documentation Pyramid:
- Quality Manual – Defines QMS policies & objectives.
- Processes – Outlines workflows at the system level.
- Procedures – Details execution steps for consistency.
- SOPs & Work Instructions – Step-by-step guides for tasks.
- Checklists & Guidelines – Ensures compliance and accuracy.
Industry Examples:
- Automotive – SOPs for quality inspections & manufacturing.
- Pharma – GMP & FDA documentation for drug safety.
- Healthcare – Patient care procedures & surgical checklists.
- Construction – Safety protocols & method statements.
- IT & Cybersecurity – Incident response procedures.
- Logistics – Shipping & compliance checklists.
The Bottom Line
Effective documentation is not just about compliance—it is a strategic tool for operational excellence. Organizations that invest in well-structured documentation enhance quality, ensure safety, and boost customer trust.
hashtag#QualityManagement hashtag#ProcessImprovement hashtag#QMS hashtag#Documentation hashtag#Compliance hashtag#BusinessExcellence hashtag#ContinuousImprovement