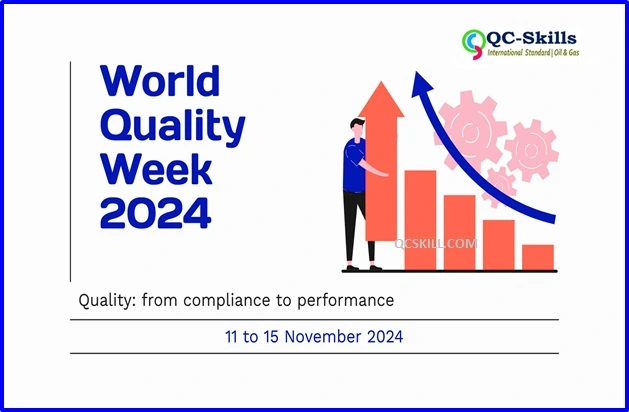
Quality by Design (QbD) is the proactive approach of embedding quality into every phase of product or process development. Rather than testing for quality at the end, QbD ensures that quality is built into the design itself, leading to more reliable, consistent, and efficient outcomes.
Why Quality by Design Matters Quality by Design reduces risks, cuts down on rework, and enhances customer satisfaction. By planning for quality from the beginning, organizations can avoid costly issues down the line, innovate confidently, and deliver results that consistently meet or exceed expectations.
Key Principles of Quality by Design
- Define Quality Goals Early Set clear, measurable quality goals from the outset, aligned with customer needs and regulatory requirements. This helps guide development efforts toward producing a robust, reliable outcome.
- Understand Customer and Process Needs Engage customers and stakeholders early to understand their requirements. Similarly, analyze process needs to ensure they align with the desired quality standards.
- Risk Assessment and Mitigation Identify potential risks throughout the design process, using tools like Failure Mode and Effects Analysis (FMEA). Addressing risks early reduces costly fixes and ensures smoother development.
- Data-Driven Decisions Leverage data and predictive analysis to make informed design choices, optimizing for quality before production begins. Use simulation and modeling to anticipate potential issues and improve design robustness.
- Test and Validate Throughout Rather than waiting for final testing, incorporate testing and validation at key stages of the design process. This allows teams to catch and address issues early, leading to a more dependable outcome.
Benefits of Quality by Design
- Reliability Built-In: Designing quality from the start ensures products and processes are reliable, reducing the chances of failures, recalls, and costly rework.
- Operational Efficiency: Addressing potential issues during the design phase minimizes downstream problems, saving time and resources. This efficiency translates into significant cost savings and faster time-to-market.
- Customer Trust and Satisfaction: When quality is consistently delivered, customers notice. Quality by Design leads to products that meet or exceed expectations, building customer loyalty and trust.
- Room for Innovation: With clear quality parameters established early, teams have more freedom to innovate confidently within a reliable framework, leading to better solutions and new possibilities.
- Compliance and Risk Reduction: Identifying and mitigating risks during design enhances regulatory compliance, reducing the chance of non-compliance issues and ensuring smoother market entry.
#QualityMonth #QualityTools #SixSigma #5S #FishboneDiagram #ControlCharts #QualityManagement #ContinuousImprovement #LinkedInCommunity