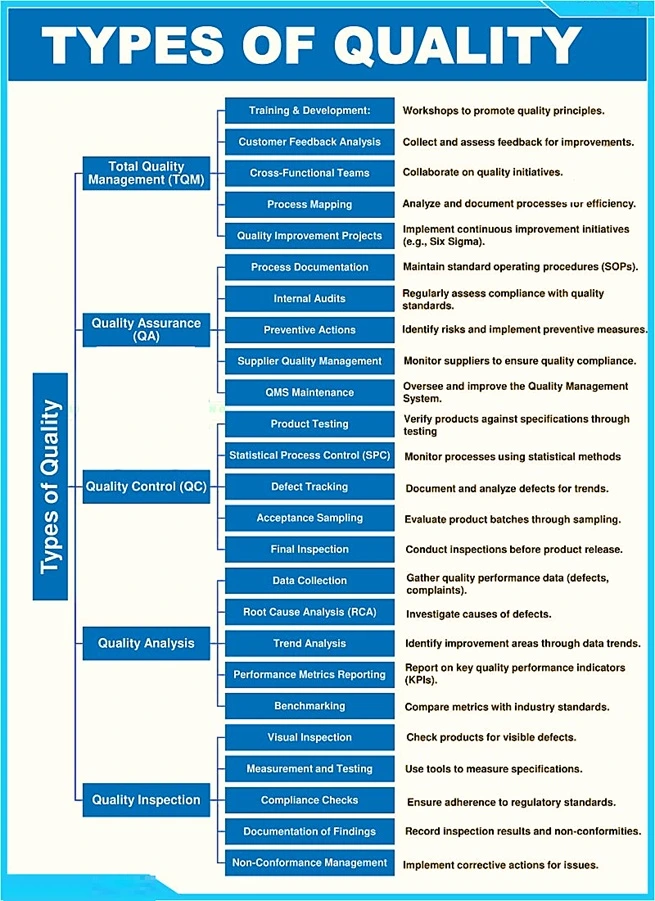
TYPE OF QUALITY FUNCTIONS AND ACTIVITIES:
Total Quality Management (TQM)
Training & Development: Workshops to promote quality principles.
Customer Feedback Analysis: Collect and assess feedback for improvements.
Cross-Functional Teams: Collaborate on quality initiatives.
Process Mapping: Analyze and document processes for efficiency.
Quality Improvement Projects: Implement continuous improvement initiatives (e.g., Six Sigma).
Quality Assurance (QA)
Process Documentation : Maintain standard operating procedures (SOPs).
Internal Audits: Regularly assess compliance with quality standards.
Preventive Actions: Identify risks and implement preventive measures.
Supplier Quality Management: Monitor suppliers to ensure quality compliance.
QMS Maintenance: Oversee and improve the Quality Management System.
Quality Control (QC)
Product Testing: Verify products against specifications through testing.
Statistical Process Control (SPC): Monitor processes using statistical methods.
Defect Tracking: Document and analyze defects for trends.
Acceptance Sampling: Evaluate product batches through sampling.
Final Inspection: Conduct inspections before product release.
Quality Analysis
Data Collection: Gather quality performance data (defects, complaints).
Root Cause Analysis (RCA): Investigate causes of defects.
Trend Analysis: Identify improvement areas through data trends.
Performance Metrics Reporting: Report on key quality performance indicators (KPIs).
Benchmarking: Compare metrics with industry standards.
Quality Inspection
Visual Inspection: Check products for visible defects.
Measurement and Testing: Use tools to measure specifications.
Compliance Checks: Ensure adherence to regulatory standards.
Documentation of Findings: Record inspection results and non-conformities.
Non-Conformance Management: Implement corrective actions for issues.