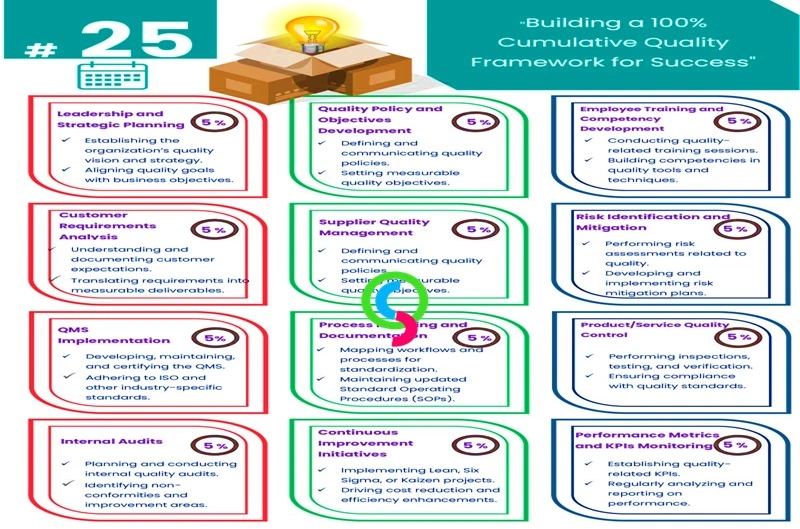
Building a 100% Cumulative Quality Framework for Success
Key Highlights of the Framework:
- 1Leadership and Strategic Planning (5%) – Setting the vision and aligning quality initiatives with business goals.
- Quality Policy and Objectives Development (5%) – Establishing clear, actionable quality goals.
- Employee Training and Competency Development (5%) – Building a skilled workforce ready to deliver excellence.
- Customer Requirements Analysis (5%) – Understanding customer expectations for tailored solutions.
- Supplier Quality Management (5%) – Strengthening partnerships for reliable supply quality.
- Risk Identification and Mitigation (5%) – Proactively addressing challenges to build resilience.
- Quality Management System (QMS) Implementation (5%) – Laying a structured foundation for quality compliance and excellence.
- Process Mapping and Documentation (5%) – Standardizing workflows for improved efficiency.
- Product/Service Quality Control (5%) – Ensuring adherence to quality standards and specifications.
- Internal Audits (5%) – Identifying improvement opportunities through assessments.
- Continuous Improvement Initiatives (5%) – Driving innovation and operational efficiency.
- Performance Metrics and KPIs Monitoring (5%) – Tracking progress to achieve strategic goals.
- Corrective and Preventive Actions (CAPA) (5%) – Resolving issues at the root to prevent recurrence.
- Customer Satisfaction and Feedback Management (5%) – Strengthening trust and loyalty through feedback.
- Innovation and Digitalization in Quality (5%) – Leveraging technology to transform quality processes.
- Compliance and Regulatory Adherence (3%) – Meeting standards to ensure consistency and reliability.
- Calibration and Equipment Maintenance (3%) – Ensuring accuracy and reliability of tools.
- Change Management (3%) – Supporting seamless transitions during transformations.
- Benchmarking and Best Practices Sharing (3%) – Learning from the best to continuously improve.
- Cross-Functional Collaboration (3%) – Enhancing efficiency through team alignment.
- EHS Integration into Quality (2%) – Merging safety, health, and environment into quality systems.
- Documentation and Records Management (2%) – Keeping essential records accessible and standardized.
- Employee Engagement in Quality (2%) – Fostering ownership and participation in quality initiatives.
- Supplier Audits (2%) – Evaluating and strengthening supplier capabilities.
- Recognition of Quality Achievements (2%) – Celebrating milestones to inspire excellence.
See more Reference – Wikipedia
#QualityManagement #LeadershipInQuality #ContinuousImprovement #RiskMitigation #EmployeeEngagement #StrategicPlanning #CustomerSatisfaction #InnovationInQuality #ComplianceMatters #SupplierManagement #ProcessExcellence #QualityCulture #DigitalTransformation #ExcellenceFramework #RecognitionOfExcellence