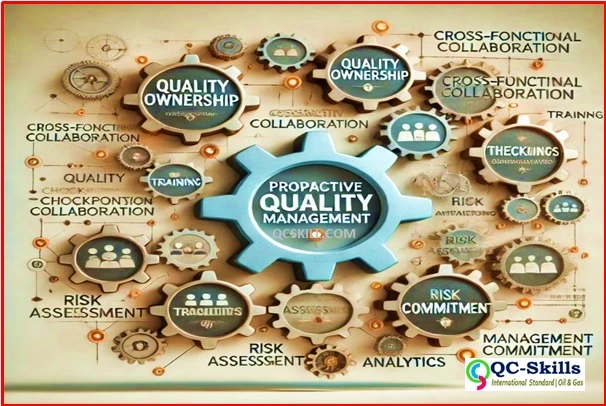
Proactive Quality Awareness: Preventing Last-Minute Uncertainties Across the Organization
In the fast-paced environments of today’s organizations, quality requirements may sometimes be unintentionally overlooked by operations and even management.
However, the repercussions of last-minute uncertainties in quality can ripple across functions, impacting overall efficiency, customer satisfaction, and brand reputation.
A proactive approach to quality awareness ensures that these critical areas aren’t left vulnerable to reactive, high-pressure decisions.
Key Challenges in Last-Minute Quality Uncertainties
When quality issues are identified at the last minute, it places the entire organization under stress, often leading to rushed fixes that may compromise overall standards and increase costs. Examples of reactive quality actions include:
- Sudden rework due to undiscovered product or process inconsistencies.
- Delayed shipments because final checks reveal unmet quality criteria.
- Customer complaints stemming from undetected issues affecting end-product usability.
- Increased internal conflict among teams due to blame allocation or resource prioritization.
To counter these challenges, organizations can adopt preventive actions that empower teams to uphold quality standards consistently.
- Clarify Quality Responsibilities for All Functions
Every department, from operations to senior management, should understand their role in upholding quality. Establish clear responsibilities. - Embed Quality Checkpoints in Processes
Develop structured checkpoints throughout production, service, or delivery cycles to catch potential issues early. Consistent reviews, self-inspections, and random audits reinforce adherence to quality standards. - Encourage Cross-Departmental Collaboration
Quality is a shared responsibility. Encourage collaboration across departments to improve communication, problem-solving, and accountability on quality measures. - Regular Training and Awareness Programs
Provide continuous training for employees and managers on evolving quality standards and their importance. Training sessions can cover how to identify potential issues and best practices for maintaining compliance. - Implement a Risk-Based Quality Approach
Use risk-based thinking to evaluate potential quality risks proactively. For each process, identify high-risk areas and apply preventive controls to avoid last-minute surprises. - Leverage Quality Analytics for Insights
Utilize data analytics to monitor quality trends, assess areas prone to non-compliance, and refine processes based on insights. Analytics enable teams to recognize and mitigate issues before they escalate. - Reinforce Management Commitment
Leadership involvement is crucial in building a proactive quality culture. Management should lead by example, emphasizing that quality excellence aligns with business success, not merely as a compliance checkbox.